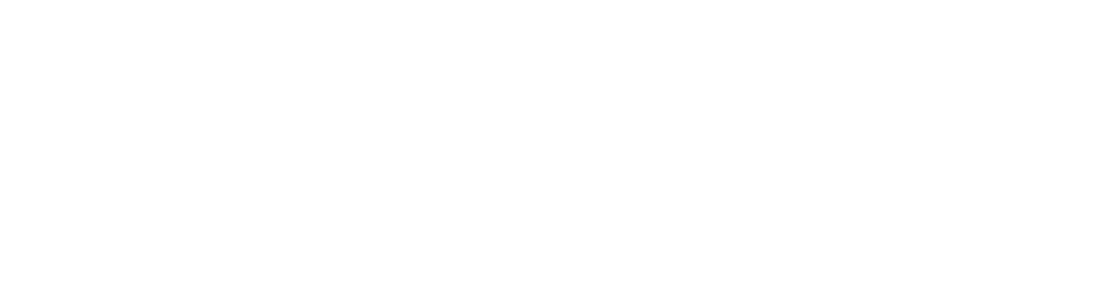
Optical Store and Lab Communication: Best Practices and Managing Expectations
Let me share with you my years of experience in the optical industry. Simple things that are misunderstood and how a better understanding of Optical Lab working can help you get the best out of your lab.
- Lab may not have All the Stock Lenses: Even the biggest of the labs with huge inventories do not have every single power in every lens type readily available in stock. They will have to order these lenses from their supplier and can easily add one working day to a job’s turnaround.
- Breakages Happen and the Whole Process has to Start Over. Breakages can randomly happen on a job regardless of its importance or time sensitivity. If a remake does happen, the whole lens-making process has to start from the beginning and the job-making process time may effectively double. It is wise to keep that in mind when promising a delivery date to your patient. Lens Shapers sends automated emails if a breakage will cause a delay in job delivery. This is useful as you can inform your customer right away.
- Polycarbonate lenses DO NOT scratch more easily. Contrariety to popular belief, polycarbonate lenses do not scratch more easily compared to plastic lenses. This myth comes from the experience that poly lenses can very easily scratch when uncoated. However, all polycarbonate lenses are completed with at least a scratch-resist coating on them which makes them equally scratch resistant as plastic lenses.
- Rushing and Quality Do Not Go Together. Whether we want to believe it or not, rushing a job may cause quality overlooks.
- There is More to Polycarbonate: Polycarbonate lenses are not just thinner than Plastic 1.5. They are also lighter in comparative weight and can be made with thinner center/edge thicknesses compared to plastic. This means that poly lenses in a given power can be thinner, lighter and flatter than comparable Plastic 1.6 lenses (sometimes even plastic 1.67). Poly is also cheaper than Plastic 1.6 but is inferior in optical quality.
- Tint with AR. The anti-Reflective process inherently causes a change in the tint shade/tone of a lens. This is hard to control or predict and can change the depth by up to 20% (lighter or darker). Keep that when ordering Match Sample Tint with AR Coating.
- Backside Only AR: We want others to see their reflection in our sunglasses, not our eyes. But we want anti-reflective coating on sunglasses because it helps avoid glare reflected from inside of the lenses. This is where Backside-only AR comes in handy. Get it for your patient’s sunglasses and they will appreciate it.
- Mirror Coating Takes Time. Mirror coating is a specialized process. Only a handful of labs actually do it in-house in Canada. These labs collect Mirror jobs over a period of days (sometimes weeks) and then run the batches. This means your Mirror Coating job can take anywhere between 2 and 4 weeks.
- Oakley Frames. Oakley frames are loved by customers and despised by the labs. Styles like Gascan are notoriously hard to edge and require specialized equipment and skillful technicians. Many smaller labs do not do this in-house. Places, where this kind of edging is done, have a higher level of breakage. Every time a breakage happens, lenses have to be remade. This means such jobs can easily take 2-4 weeks to make and have a higher cost associated with them. Price and promise such jobs accordingly.
- ETA Depends on the Number of Processes: The number of processes increases the turn-around time. It is useful to get a sense of how long each process (surface, tint, coat, edge) takes in your lab. Talk to the lab staff and ask them. This will help you quickly calculate the expected turn-around. Lens Shapers’ ordering portal displays ETA (Estimated Time of Arrival) for every job you place with us. This helps manage the patient’s expectations in a smooth manner.
- Not all Jobs will Cut-out in Stock Lenses: Stock lenses mostly come in 70mm diameter. For positive sphere powers, this diameter is usually 65mm. The lab will only inform you of a job not cutting out in stock lenses AFTER they have entered the job data in their computer system or maybe even after tracing the frame and trying to block the lenses. This means valuable time is wasted before the lab comes back to you asking to surface the job. You can save this time by quickly calculating the cut-out yourself using a regular calculator or even better an Optical Calculator and then order in stock or surfaced lenses accordingly.
- Lab cannot Guess Frame’s Base Curve: If a job’s frame has a higher than normal (BC 6) inform the lab through your order form. This will help them make lenses in suitable base curve. Failure to do may result in lenses being made in a generally flatter base curve and only caught at the time of edging wasting valuable time.
- Be Careful with Ordering Higher Base Curves: Ordering base curves over 6-8 is generally impractical, especially for high minus powers. If a sunglasses’ demo lenses base curve measures over 8, let the lab decide (unless the doctor specifies a base curve) which base curve will be a good balance between final lens thickness and final frame curvature.
- Stock Lenses have Fixed Base Curves: When edging stock lenses into a frame, the base curve of the stock lens mostly dictates the resulting shape of the frame. Stock lenses are created flat by design and many times, this causes the frame’s temples to spread out. Frames are then bent either at the temples or nasal to bring their shape back. While this works most of the time, in some cases this results in an aesthetically displeasing frame shape and the solution is to surface the lenses in an appropriate base curve. This costs more and should be kept in mind when pricing a job.
Managing Patient Expectations
- Realistic Turn-around Times: Be upfront with patients about the turn-around time for their orders. Explain that quality lenses take time to manufacture and that rushing the order can compromise the quality of the product.
- Patient-Owned Frames: Labs do not compensate for damage caused to old frames. You should keep that in mind and communicate it to the patient beforehand when taking up jobs with patients’ owned frames.
- Quality Control: Once the lenses have arrived, inspect them carefully to ensure they meet your specifications. Check the lenses for accuracy, visual quality, and durability. Remember that at the end of the day, legally it is the Optician’s responsibility that the job meets all requirements.
Recent Posts